Public Relations
Auf dieser Seite, erhalten Sie einen Überblick zu den bisher veröffentlichten Pressemitteilungen aus den Forschungs- und Entwicklungsarbeiten des iwb.
Sollten Sie Interview- oder Filmtermine, Foto- oder Textmaterial wünschen, steht Ihnen unser Service-Center Public Relations sehr gerne zur Verfügung.
Das iwb begrüßt Prof. Dr.-Ing. Rüdiger Daub zum 01. Juni 2021 als neuen Institutsleiter an der Seite von Prof. Dr.-Ing. Michael F. Zäh
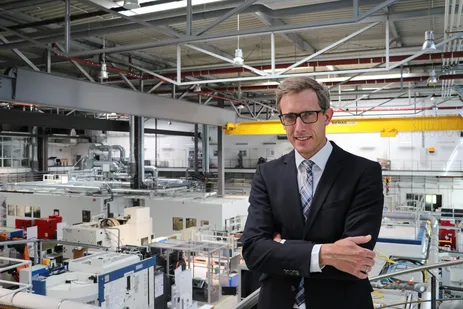
Mit Wirkung zum 01. Juni 2021 folgt Prof. Dr.-Ing. Rüdiger Daub als Leiter des Instituts für Werkzeugmaschinen und Betriebswissenschaften (iwb) der Technischen Universität München auf den im Oktober 2020 emeritierten Prof. em. Dr.-Ing. Gunther Reinhart. Als Ordinarius des am iwb neu eingerichteten Lehrstuhls für Produktionstechnik und Energiespeichersysteme wird Rüdiger Daub somit Prof. Dr.-Ing. Michael F. Zäh in der Institutsleitung unterstützen. In einem neuen Kooperationsmodell in gemeinsamer Berufung mit der Fraunhofer Gesellschaft übernimmt er damit die Verantwortung für die Batterieforschung am iwb. Mit seiner langjährigen Erfahrung in der Batteriezellenfertigung bei BMW wird Herr Daub nun zukünftig vor allem die Forschung in diesem Bereich am Institut vorantreiben.
Nach beinahe zehn Jahren in der Wirtschaft kehrt Prof. Dr.-Ing. Rüdiger Daub am 01. Juni 2021 in die Forschung zurück. Seiner Berufung als Ordinarius des am Institut neu eingerichteten Lehrstuhls für Produktionstechnik und Energiespeichersysteme gehen langjährige Erfahrungen sowohl am iwb selbst als auch im Bereich der Fertigung von Batteriezellen voraus: Rüdiger Daub promovierte 2012 am Institut für Werkzeugmaschinen und Betriebswissenschaften und stieg direkt nach seiner Promotion bei der BMW Group im Bereich Technologieentwicklung und Prototypenbau ein. Zuletzt war er als Leiter Technologieentwicklung und Prototypenbau für die Produktion von Lithium-Ionen-Elektroden verantwortlich.
An der Seite von Prof. Dr.-Ing. Michael F. Zäh, Ordinarius des Lehrstuhls für Werkzeugmaschinen und Fertigungstechnik, wird Prof. Dr.-Ing. Rüdiger Daub nun am iwb ab dem 01. Juni 2021 neue Schwerpunkte bei diesem immer wichtiger werdenden Forschungsthema setzen. „Das Berufungsverfahren war ein langwieriges, deshalb haben wir uns zu Beginn des Jahres umso mehr gefreut, als wir um die Nachfolge durch unseren ehemaligen wissenschaftlichen Mitarbeiter Herrn Daub erfuhren – das ist sowohl fachlich als auch menschlich ein großer Gewinn für unser Institut“, sagt Prof. Dr-Ing. Michael F. Zäh. Rüdiger Daub folgt damit auf Prof. em. Dr.-Ing. Gunther Reinhart, der das iwb 27 Jahre leitete und in dieser Zeit den Wissenschaftsbereich Verarbeitungstechnik im Fraunhofer IGCV aufbaute, dessen Leitung Herr Daub übernimmt.
Stabile Schweißnähte für Luft- und Raumfahrt
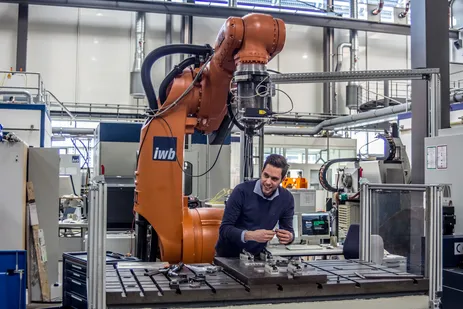
Bild: Giacomo Costanzi / TUM
Messungen an der Forschungs-Neutronenquelle helfen bei der Entwicklung intelligenter Schweißgeräte
Die Schweißnähte des riesigen Treibstofftanks einer Rakete müssen beim Start immense Kräfte aushalten. Für solche besonders stabilen Nähte wird das Verfahren des Rührreibschweißens genutzt. Wissenschaftler der Technischen Universität München (TUM) wollen das Verfahren effizienter machen. Sie nutzten dabei die Positronen der Forschungs-Neutronenquelle Heinz Maier-Leibnitz (FRM II), um atomare „Löcher“ im Material präzise zu lokalisieren.
Das Verfahren des Rührreibschweißens wird immer häufiger bei Bauteilen eingesetzt, bei denen die Nähte besonders dicht und stabil sein müssen. Etwa im Flugzeugrumpf, im Kühlsystem des Autos oder auch beim Treibstofftank einer Rakete. Im Gegensatz zu anderen Schweißverfahren benötigt das Rührreibschweißen kein zusätzliches Schweißmaterial, und die Temperaturen bleiben in der Regel unter der Schmelztemperatur. Damit ist das Verfahren besonders für temperaturempfindliche Materialien wie das leichte Aluminium geeignet.
Sind die Bauteile fest eingespannt, wird an deren Grenzfläche der schnell drehende Schweißstift des Schweißgerätes entlanggeführt. Der Stift weicht das Material durch Reibungswärme auf, ohne es zu schmelzen. Während sich der Stift voran bewegt, verrührt er die beiden Bauteile an der Grenzfläche und sorgt nach dem Abkühlen für eine besonders feste Naht.
Das Problem bei dem erst 30 Jahre alten Verfahren sind fehlende Erfahrungswerte. Bei jedem neuen Bauteil und Material müssen die Einstellungen des Geräts durch Ausprobieren bestimmt werden. Durch eine automatische Regelung, welche die Einstellungen selbst bestimmt und anpasst, würde sich die Effizienz des Verfahrens enorm verbessern. Dafür hat Dr. Andreas Bachmann in seiner Forschungsarbeit an der TUM ein Regelungskonzept entwickelt.
Positronen finden „Löcher“ im Metall
Zunächst untersuchte Bachmann anhand einer speziellen Aluminiumlegierung, die in der Raumfahrt eingesetzt wird, wie genau die Temperatur und Schweißgeschwindigkeit den Prozess beeinflussen. Dazu nutzte er die weltweit intensivste Positronenquelle NEPOMUC der Forschungs-Neutronenquelle Heinz Maier-Leibnitz (FRM II). „Mit der Methode der Doppler-Verbreiterungsspektroskopie konnten wir die Defekte im Metall in und nahe der Schweißnaht finden“, sagt Bachmann.
Forschende schießen bei der Doppler-Verbreiterungsspektroskopie Positronen in das Metallgitter. Hier werden sie von den ebenfalls positiv geladenen Atomrümpfen im Gitter abgestoßen und bewegen sich von selbst zu Leerstellen, wo sie auf ihr Antiteilchen, ein Elektron, treffen. Die Teilchen löschen sich gegenseitig aus und senden dabei Energiestrahlen aus, die wiederum detektiert werden. Die gemessenen Strahlen geben Auskunft über die Position und Häufigkeit von atomaren Leerstellen.
Defekte sind temperaturabhängig
Die Forschenden fanden bei ihren Untersuchungen weniger Defekte bei höheren Schweißtemperaturen um die 500 Grad Celsius. „Im Vergleich zu anderen Schweißverfahren sind 500 Grad allerdings immer noch sehr niedrig“, erklärt Bachmann. „Es ist also so: Eine geringere Schweißtemperatur ist für die temperaturempfindlichen Materialien natürlich besser; wenn sie zu gering ist, wirkt sich das aber negativ auf die Festigkeit der Naht aus.“ Die ideale Schweißtemperatur ist für die Materialien unterschiedlich und muss jeweils bestimmt werden.
Mit diesen Erkenntnissen entwickelte Bachmann eine Regelung, bei der die optimale Temperatur eingestellt wird. Ein Sensor misst die Temperatur in Echtzeit. Mithilfe eines Algorithmus wird bestimmt, wie schnell sich das Werkzeug drehen muss, damit die Abweichung zwischen Soll- und Ist-Wert 0 beträgt. „Eine Schweißnaht mit Regelung war im Test 1,5-Mal so fest wie ohne Regelgung", erklärt Bachmann.
Außerdem zeigte er, dass theoretisch auch eine Regelung ohne Temperatursensoren möglich wäre. Dabei wird der Widerstand beim Drehen des Schweißstiftes gemessen und auf diese Weise die Temperatur bestimmt. „Je wärmer das Metall ist, desto leichter lässt es sich umformen, beziehungsweise mit dem Werkzeug verrühren“, erklärt Bachmann, der mittlerweile in der Industrie arbeitet. „Wie leicht oder wie schwer sich das Metall verrühren lässt, kann über das an der Spindel, also den Motor, der das Werkzeug antriebt, anliegende Moment gemessen werden.“ Dieser Ansatz könnte weiterentwickelt werden, um den Einsatz dieser Regelung in der Praxis zu erleichtern.
Publikation:
Bachmann, A.; Gigl, T.; Hugenschmidt, C. P.; Zaeh, M. F.: Characterization of the microstructure in friction stir welds of EN AW-2219 using coincident Doppler-broadening spectroscopy. In: Materials Characterization 149, (2019), S. 143 – 152.
https://doi.org/10.1016/j.matchar.2019.01.016
Quelle: TUM Corporate Communications Center
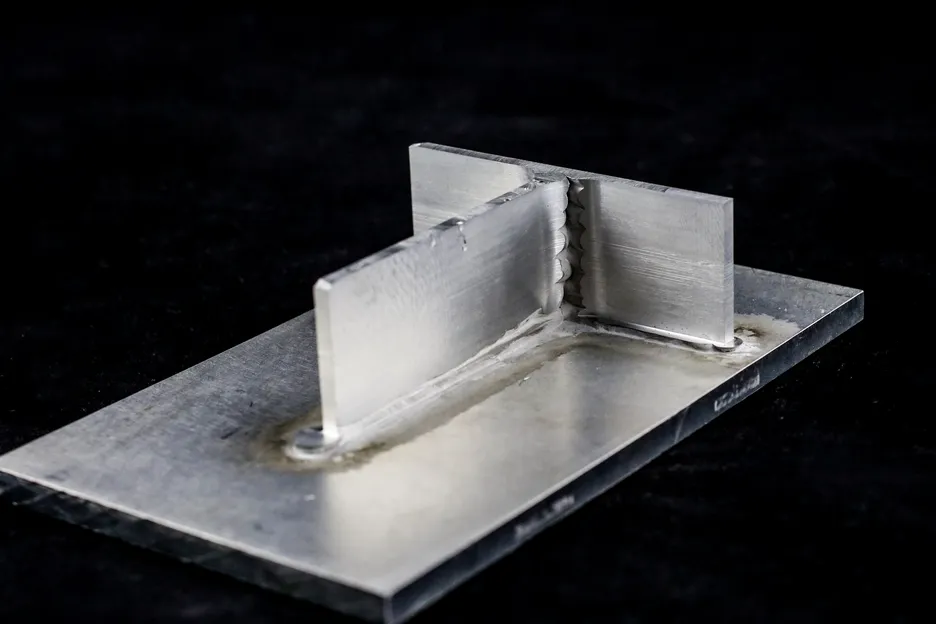
24. – 26.09.2019 – Das Additive Manufacturing Laboratory (AMLab) auf der Experience Additive Manufacturing Augsburg (EAM) 25.09.2019 – Seminar für Additive Fertigung
Lernen Sie am Stand C202 der Fachmesse zur Additiven Fertigung EAM das AMLab kennen. Das AMLab wurde 2012 vom Fraunhofer IGCV und dem iwb mit dem Ziel gegründet, die Anlagen- und Prüftechnik gemeinschaftlich zu nutzen sowie zusammen an verschiedenen Verfahren zu forschen, z. B. dem Laser-Strahlschmelzen oder der lichtbogen- und drahtbasierten Additiven Fertigung. Experimentelle und analytische Untersuchungen tragen dazu bei, das Prozessverständnis dieser Verfahren zu erweitern und mit innovativen Ansätzen das Anwendungsspektrum zu erweitern. Dabei werden die Schritte (Pre-, In- und Post-Prozess) der additiven Prozesskette betrachtet. Zu den Anwendungsfeldern (iwb) zählen unter anderem die Medizintechnik, die Luft- und Raumfahrttechnik oder die Batterieproduktion. Bei den Bestrebungen im Bereich der Medizintechnik geht es beispielsweise darum, Implantate so zu gestalten und herzustellen, dass deren Verformungseigenschaften möglichst dem natürlichen Verhalten des Knochens entsprechen. Das Fraunhofer IGCV stellt auf der Messe zudem neue Leichtbaukonzepte vor. Ein Getriebe zeigt das Zusammenspiel aus Additiver Fertigung, Composite- und Gießereitechnik. Aus dem Themenkomplex der Additiven Fertigung von Metallen werden Beispielbauteile ausgestellt, welche erfolgreiche Multimaterialverarbeitung, Funktionsintegration sowie hochkomplexe bionische Designs demonstrieren.
Parallel zur Messe findet am 25. September 2019 das 23. Augsburger Seminar für Additive Fertigung statt
Des Weiteren findet das 23. Augsburger Seminar für Additive Fertigung im Rahmen der EAM statt. Veranstaltungspartner sind hierbei das Fraunhofer IGCV und das iwb der TUM. Das diesjährige Thema lautet: „Perspektiven der Additiven Fertigung: Reproduzierbarkeit und neue Technologien“. Das Seminar bietet gerade für mittelständische Unternehmen die Chance, einen Überblick über alle Elemente der Prozesskette für den erfolgreichen Einsatz der Additiven Fertigung zu erlangen – von der additiv-gerechten Produktkonzeption bis zur Veredelung additiv gefertigter Bauteile. Was vor einigen Jahren noch als Fertigungsverfahren für den Prototypenbau galt, wird heute als ernst zu nehmende Alternative für die flexible Serienproduktion angesehen. Das Augsburger Seminar soll sowohl der Industrie als auch der Forschung eine Plattform bieten, um sich über aktuelle Problemstellungen und Themen der Zukunft auszutauschen. Das Seminar verbindet dabei Vorträge von erfahrenen Anwendern und Vertretern aus der Industrie mit innovativen Ansätzen aus der Wissenschaft.
Hochkarätige Referenten sind vertreten, wie beispielsweise:
Dr.-Ing. Wilhelm Meiners, Trumpf GmbH, Expert Additive Manufacturing und SLM Patentinhaber; Prof. Dr.-Ing. Gerd Witt, Universität Duisburg-Essen, Inhaber Lehrstuhl für Fertigungstechnik; Andy Middleton, Stratasys, Executive Vice President und Andreas Berkau, Oerlikon, Senior Vice President AM Strategy – Additive Manufacturing. Das Seminar findet in den Tagungsräumen des Messegeländes Augsburg statt.
Weitere Informationen zum Seminar sowie die Möglichkeit zur Anmeldung via Online-Formular finden Sie unter https://www.amlab.de/am-seminar2019
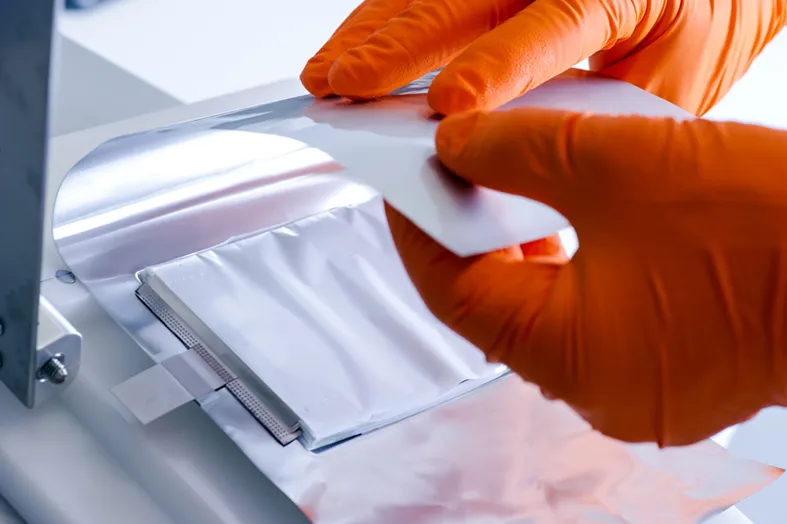
Zum 01. Juli 2019 wurde das Institut für Werkzeugmaschinen und Betriebswissenschaften (iwb) der Technischen Universität München um die Themengruppe "Batterieproduktion" erweitert. Dadurch wird die Kompetenz in der Batterieforschung gebündelt und weiter ausgebaut. Die neue Themengruppe setzt den Fokus mit bereits 11 Mitarbeiterinnen und Mitarbeitern auf die gleichen Ziele, die auch die Bundesregierung verfolgt – die Stärkung der Batterieforschung und -produktion von morgen.
Leistungsfähige elektrochemische Energiespeicher sind für Anwendungen in der Elektromobilität und der stationären Energiespeicherung von großer Bedeutung. Hierfür sind die Verbesserung der gravimetrischen und volumetrischen Energiedichte sowie die Reduktion der Produktionskosten ausschlaggebend. Erst ein vertieftes Prozessverständnis über die Herstellung von Lithium-Ionen-Batterien (LIB) ermöglicht die Produktion verbesserter und kostengünstiger Batteriezellen.
Die im Juli 2019 neugegründete Themengruppe Batterieproduktion beschäftigt sich mit der Fertigung von innovativen Batteriezellen. Kern der Arbeiten ist die Prozessentwicklung und die Optimierung aller Prozesse innerhalb der Batterieproduktion. Vom Mischen der Elektrodenmaterialien bis hin zur Formierung der fertigen Zellen und der Batteriemodulmontage werden alle Schritte in-house an der Forschungsproduktionslinie des iwb durchgeführt. Die Forschungsschwerpunkte der Themengruppe Batterieproduktion sind:
• Elektrodendesign und -herstellung
Im Forschungsfeld Elektrodendesign und -herstellung beschäftigen sich die Mitarbeiterinnen und Mitarbeiter intensiv mit neuen Elektrodendesigns (von Slurry-Rezepturen bis zu Elektrodenstrukturen) und der Verarbeitung neuartiger Elektrodenmaterialien. Kathodenseitig stehen vor allem kobaltarme Materialien auf NMC-, NCA-Basis sowie prälithiierte manganreiche Hochvoltspinelle im Fokus der Forschung. Für Anodenmaterialien liegt der Forschungsschwerpunkt auf Silizium-Kompositen und der Prälithiierung von Anoden.
• Zellproduktion und -qualität
Das Forschungsfeld Zellproduktion und -qualität beschäftigt sich intensiv mit der Zellassemblierung und der Charakterisierung großformatiger Batteriezellen. Am iwb wird an den Prozessschritten Elektrodenschneiden (Laserschneiden und Stanzen), automatisierte Stapelbildung, Kontaktierung, Elektrolytbefüllung und Formierung geforscht. Um entlang der Prozesskette eine hohe Produktivität, eine gute Qualität bei geringen Kosten, gewährleisten zu können, setzt das iwb auf innovative Qualitätssicherungsmethoden und eine datenbasierte Prozessüberwachung.
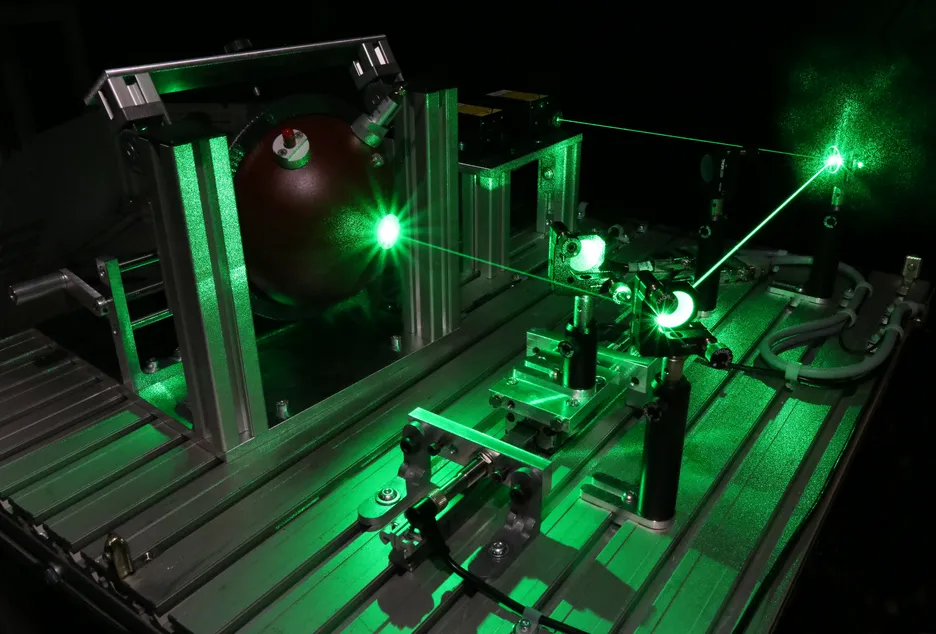
„Smart Photonics“ lautet das Motto, unter dem die Bayerisches Laserzentrum GmbH (blz), das Institut für Werkzeugmaschinen und Betriebswissenschaften (iwb) der Technischen Universität München und der Lehrstuhl für Photonische Technologien (LPT) der Friedrich-Alexander-Universität Erlangen-Nürnberg in Kooperation mit der Messe München zukunftsweisende Laseranwendungen für die intelligente Produktion von morgen vorstellen. Besondere Highlights der Sonderschau, die im Rahmen der LASER World of PHOTONICS vom 24. bis 27. Juni 2019 in München stattfindet, sind dieses Jahr wieder zwei Laser-Live-Demonstrationen zu ausgewählten Trendthemen.
Alle interessierten Journalistinnen und Journalisten sind herzlich eingeladen, sich am Dienstag, den 25. Juni um 11:30 Uhr bei einem Pressebrunch auf der Sonderschau „Photons in Production“ (Halle A3, Stand 251) über aktuelle Forschungsarbeiten der beteiligten Einrichtungen zu informieren.
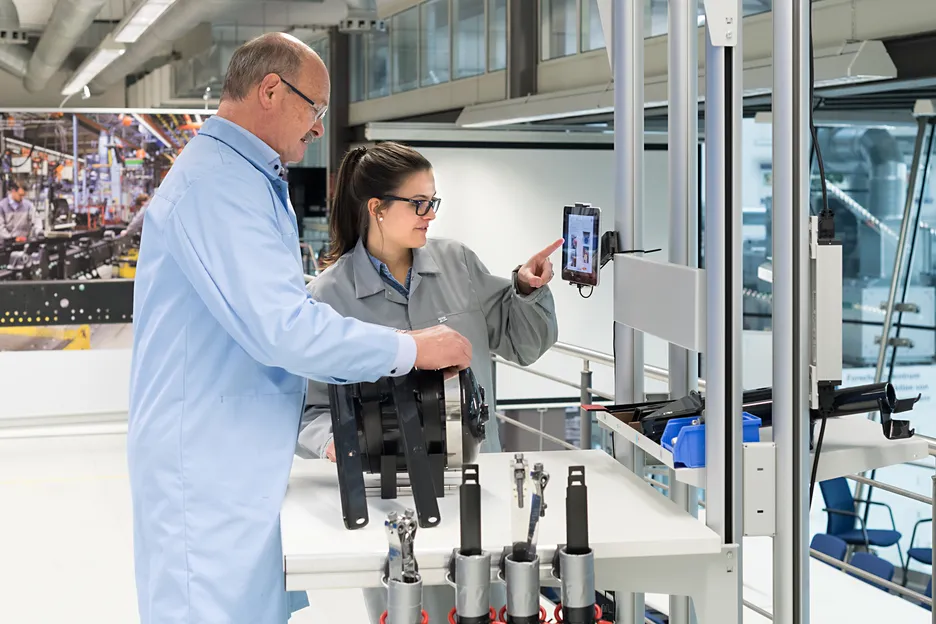
Die Digitalisierung verändert das Arbeitsumfeld: Produktionsprozesse werden von Künstlicher Intelligenz gesteuert und Roboter übernehmen neue Aufgaben. Auf der diesjährigen Hannover Messe, einer der wichtigsten Industriemessen der Welt, zeigen Wissenschaftlerinnen und Wissenschaftler des Instituts für Werkzeugmaschinen und Betriebswissenschaften (iwb) der Technischen Universität München (TUM) herausragende Forschungsprojekte auf dem Gemeinschaftstand der Bayern Innovativ GmbH in Halle 2, Stand A52. Zu den Highlights zählen eine Live-Demonstration zur ressourceneffizienten Fertigung von großvolumigen Luftfahrt-Komponenten.
Komponenten für Flugzeuge und Autos, individuelle medizinische Implantate oder sogar Fassaden und Häuser: Die Additive Fertigung, umgangssprachlich auch 3D-Druck genannt, revolutioniert die Produktionstechnik. Eine Fachkonferenz, die am 10. und 11. Oktober an der Technischen Universität München (TUM) stattfindet, verdeutlicht die Bandbreite dieser Technologie und gibt Einblicke in die breit aufgestellte Expertise der TUM.
Die Additive Fertigung umfasst verschiedene Verfahren, bei denen die Komponenten durch schicht- oder elementweises Hinzufügen von Werkstoffen aufgebaut werden. Diese Art der Fertigung hat viele Vorteile: Die Konstrukteure haben mehr Freiheiten bei der Gestaltung, bestimmte Funktionen können direkt im Bauteil integriert werden, und die Herstellung individuell angepasster Produkte ist auch in kleinen Mengen wirtschaftlich.
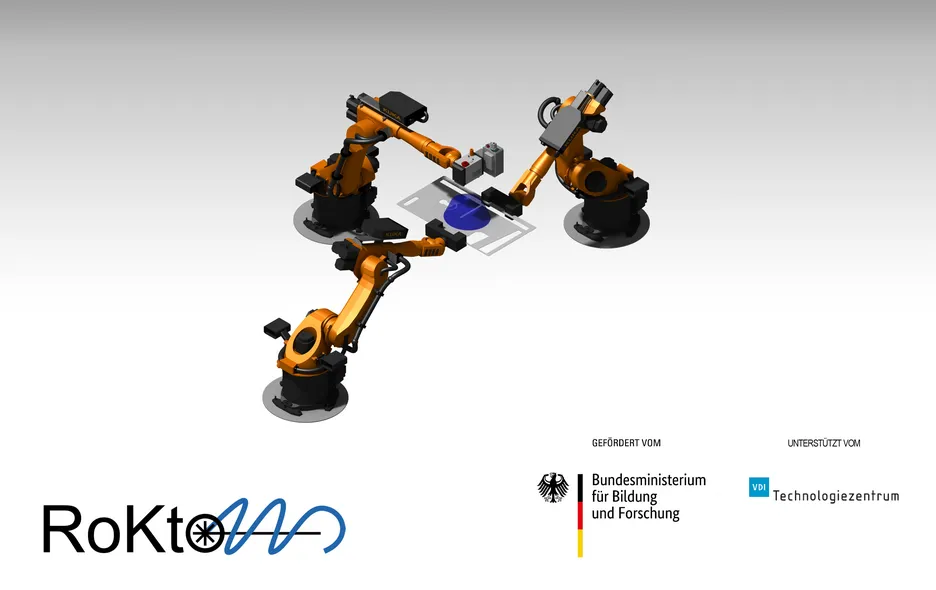
Mit der Flexibilisierung der Prozessketten im Karosseriebau den Marktveränderungen positiv entgegenblicken? Das Forschungsprojekt „RoKtoLas - Robotergeführte, scannerbasierte optische Kohärenztomografie für das Remote-Laserstrahlschweißen zur Flexibilisierung von Prozessketten im Karosseriebau“ hat zum Ziel, die Produktion von Automobilkarosserien in Zukunft flexibler zu gestalten. Mit einem Gesamtprojektvolumen von 4,8 Mio € angesetzt, sollen die Produktionsschritte flexibler und individueller gestaltet werden können. Das bisher eingesetzte Widerstandpunktschweißen soll in Zukunft durch ein innovatives Füge- und Spannkonzept substituiert werden.
Die Individualisierung von Produkten ist auch im Automobilbau ein wichtiger Faktor der Marktwirtschaft. Jedoch stehen hier eine stetig steigende Variantenvielfalt aufgrund der zunehmenden Elektrifizierung sowie die immer schneller werdenden Produktlebenszyklen gegenüber. Um einen Innovationssprung im automobilen Karosseriebau zu erzielen, wird im Forschungsprojekt RoKtoLas eine Flexibilisierung in der Produktion von Rohkarosserien angestrebt. Das soll durch eine Technologiesubstitution im Bereich der Fügetechnik erreicht werden. Das konventionelle Widerstandspunktschweißen soll in Teilen durch das Remote-Laserstrahlschweißen ersetzt werden.
Innovationssprung für den automobilen Karosseriebau
Ein neuartiges, auf Robotern basiertes Spannsystem ermöglicht eine Bauteilkonstruktion, welche hinsichtlich Leichtbau und Funktionsintegration optimiert und auf das Laserstrahlschweißen angepasst werden kann. Mit Hilfe eines innovativen Sensorikkonzepts für das Laserstrahlschweißen sollen hochflexible Produktionsanlagen, die auch unterschiedlichste Bauteile prozesssicher fügen können, umgesetzt werden. Das Sensorikkonzept, basierend auf der optischen Koheränztomografie (OCT), soll dabei eine vollumfängliche Online-Prozessüberwachung ermöglichen. So können Fügevorrichtungen in Zukunft nicht nur hochflexibel eingesetzt werden, sondern auch der Prozess des Remote-Laserstrahlschweißens wird fortlaufend überwacht und auf die Anforderungen der Fügestelle adaptiert. Das neue Sensorikkonzept generiert umfangreiche Prozessdaten im Sinne der vernetzten Produktion und stellt somit die Voraussetzung für die Umsetzung einer hochflexiblen Fertigung dar. Mit diesem Konzept soll es zukünftig möglich sein, neue Fahrzeugvarianten und -derivate ohne aufwendige Umbaumaßnahmen in die bestehende Produktionsarchitektur zu integrieren. Zudem ermöglicht der Wegfall von massiven und bauteilangepassten Spannvorrichtungen eine zügige und somit kostengünstige Anpassung der Fertigungslinie bei Änderungen am Fahrzeugdesign. Die im Forschungsprojekt RoKtoLas gewonnenen Erkenntnisse sollen am Ende des Projekts anhand eines Funktionsdemonstrators einer flexiblen Fertigungszelle zusammengeführt werden.
Zum Projekt
Zusammenfassend strebt das Konsortium im Projekt RoKtoLas eine Flexibilisierung in der Produktion von Rohkarosserien an. Dazu soll das vorrichtungsbasierte Widerstandspunktschweißen durch das hochflexible Remote-Laserstrahlschweißen substituiert werden. Unterstützt durch ein innovatives Sensorikkonzept werden so hochflexible Produktionsanlagen ermöglicht, die unterschiedlichste Bauteile prozesssicher fügen können. Das Vorhaben wird mit Mitteln des Bundesministeriums für Bildung und Forschung (BMBF) im Rahmen des Förderprogramms Photonik Forschung Deutschland unter dem Förderkennzeichen 13N14555 gefördert und vom VDI Technologiezentrum (VDI TZ) betreut.
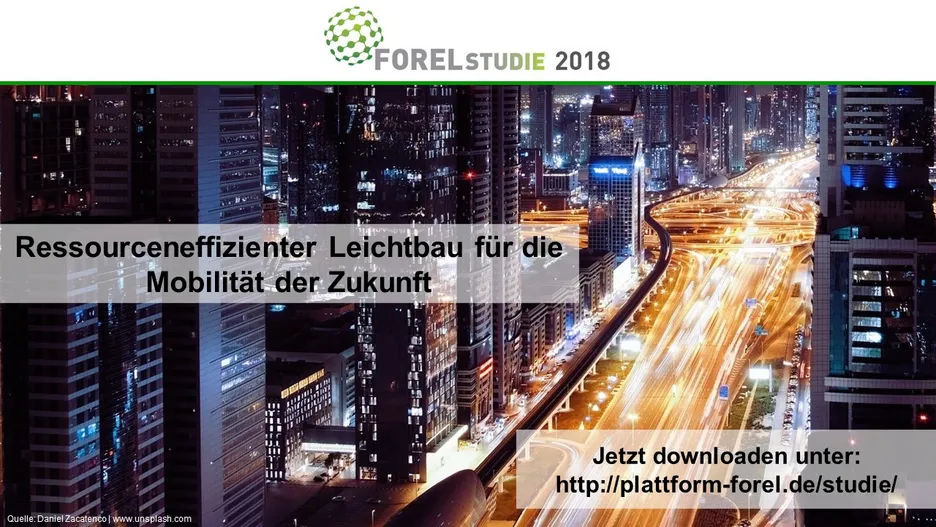
Mit der zweiten Studie zum Entwicklungsbedarf im Bereich des Leichtbaus und der Elektromobilität zeigen Wissenschaftlerinnen und Wissenschaftler aus dem deutschlandweiten Kooperationsprojekt FOREL neue Wege zur Mobilität der Zukunft.
Innovative Fertigungstechnologien von morgen sind ein entscheidender Faktor für die Mobilität der Zukunft. Mit der Anfang 2018 veröffentlichten Studie „Ressourceneffizienter Leichtbau für die Mobilität: Wandel – Prognose – Transfer“ des Forschungs- und Technologiezentrums für ressourceneffiziente Leichtbaustrukturen der Elektromobilität (FOREL) werden innovative Fertigungstechnologien für kommende Fahrzeugarchitekturen adressiert. Die Studie zeigt Defizite auf und leitet Handlungsbedarfe ab. Dieses Jahr ist die Studie mit ausführlichen Interviews mit Entscheidungsträgern aus der Automobil- und Zulieferindustrie sowie zugehörigen Dienstleistern ergänzt und bietet so wesentliche Hintergrundinformationen.
Funktionsintegrativer Leichtbau als Schlüsselrolle
Aufbauend auf den Ergebnissen der FOREL-Studie aus dem Jahr 2015 und den inzwischen zehn FOREL-Technologieprojekten wird aus der aktuellen Studie ersichtlich, dass vor dem Hintergrund des Wettbewerbs zwischen konventionellen und neuen Antriebskonzepten, sich wandelnder Nutzungsprofile sowie neuer Bauweisen besonders der funktionsintegrative Systemleichtbau als Querschnittsdisziplin weiterhin eine Schlüsselrolle spielen wird. Ein deutlich zunehmender Entwicklungsdruck hinsichtlich der Umweltfreundlichkeit zukünftig erzeugter Fahrzeuge wird von den befragten Experten erwartet.
Nachhaltigkeit im Leichtbau ein großer Faktor
Die Ergebnisse zeigen, dass sich die Entscheidung für oder gegen einen Leichtbauwerkstoff in Zukunft verstärkt nach den Auswirkungen auf den Produktlebenszyklus richten wird. Jedoch zeichnet sich in der Studie auch ab, dass zum einen die Ökologie ein klarer Faktor zur Entscheidung ist, zum anderen aber auch Hemmnisse, wie der hohe notwendige personelle und finanzielle Aufwand, erkennbar sind.
Langfristige Entwicklung von Leichtbauanwendungen
Die FOREL-Studie 2018 gibt wichtige Impulse für die zukünftige Ausrichtung der Plattform FOREL und die anwendungsnahe Weiterentwicklung des Leichtbaus für die Mobilität von Morgen. Aus der Analyse der Umfrageergebnisse und der Experten-Interviews gehen komplexe Aufgabenstellungen hervor, die weit über die herkömmliche Technologieentwicklung hinausgehen. Neben der Initiierung weiterer Technologieprojekte unter dem Dach von FOREL dienen die in der FOREL-Studie 2018 formulierten Szenarien der Fortschreibung der Leichtbau-Roadmap der Nationalen Plattform Elektromobilität (NPE).
Die FOREL-Studie 2018 wurde unter Leitung des Instituts für Leichtbau und Kunststofftechnik (ILK) der TU Dresden in Zusammenarbeit mit dem Laboratorium für Werkstoff- und Fügetechnik (LWF) der Universität Paderborn, dem Institut für Werkzeugmaschinen und Betriebswissenschaft (iwb) der Technischen Universität München, dem Institut für Aufbereitungsmaschinen (IAM) der Technischen Universität Bergakademie Freiberg und dem Institut für Umformtechnik und Leichtbau (IUL) der TU Dortmund entwickelt.
Die FOREL-Studie ist online über www.plattform-forel.de/studie als Buch bestellbar oder kann als PDF-Datei heruntergeladen werden.
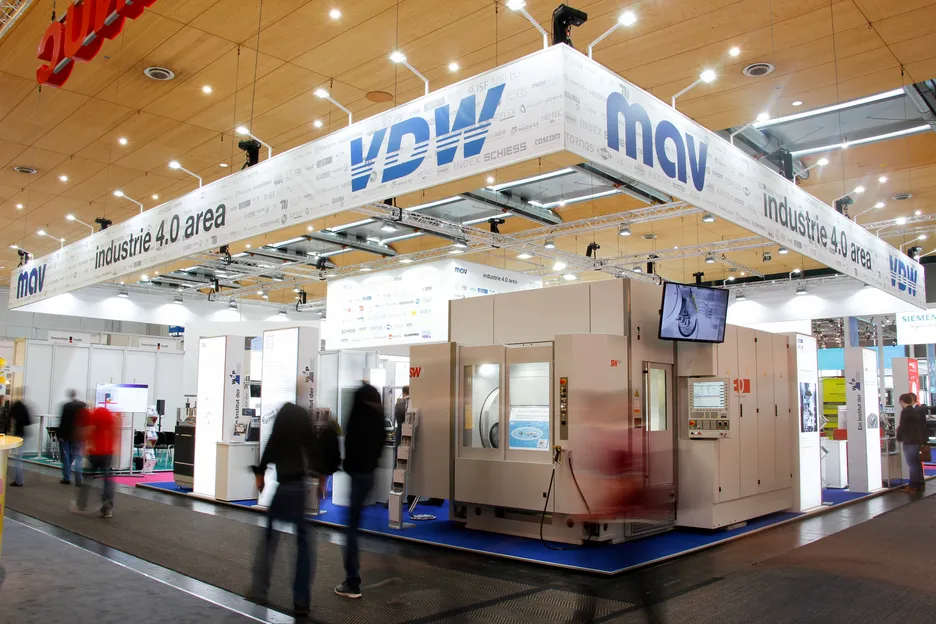
Als Schaufenster für den internationalen Markt wartete die EMO 2017 mit interessanten Diskussionen und erfolgsversprechenden Gesprächen auf. Nach sechs aufregenden Messetagen verabschiedeten sich mehr als 2.200 internationale Hersteller aus Hannover.
Auf der vom VDW und dem Konradin Verlag organisierten Sonderschau „mav industrie 4.0 area“ erhielten Gäste der EMO Hannover 2017 einen Einblick, wie sie in Zeiten von Digitalisierung und Vernetzung in der Produktion einen größtmöglichen Kundennutzen generieren können. Zusammen mit nationalen und internationalen Technologieführern präsentierte das iwb die Ergebnisse des Forschungsprojektes „BaZMod“. Hauptziel des Projektes war die Entwicklung einer standardisierten, herstellerunabhängigen Schnittstelle zur Einbindung von Cyber-Physischen Zusatzmodulen in Werkzeugmaschinen. Diese standardisierte Schnittstelle integriert dabei die mechanische und die elektrische Ankopplung des Werkzeugs und stellt somit die Basis für den bidirektionalen Datenaustausch sowie die Energieübertragung dar.
Mit der Ausstellung einer Werkzeugmaschine des Typs BA422 der Firma SW mit zwei integrierten BaZMod-Spindeln konnte dem Fachpublikum live die Funktionsweise der Schnittstelle präsentiert werden. Das Interesse an der neuen Schnittstelle war groß: Hersteller von Werkzeugmaschinen, Spindeln und Messmitteln möchten zukünftig die BaZMod-Schnittstelle einsetzen, um sowohl die Produktiviät als auch die Flexibilität ihrer Produkte zu steigern.
Fachvortrag gibt Einblick in die im Projekt BaZMod entwickelte Technologie
Auf der Sonderschau „mav industrie 4.0 area“ stellten Expertinnen und Experten führender Forschungsinstitute sowie Unternehmen ihre Themen dem interessierten Publikum im Rahmen eines Forums vor. Auch der Fachvortrag von Prof. Dr.-Ing. Michael F. Zäh, Leiter des iwb, traf mit seinem Thema den Nerv der Zeit. Er zeigte in seinem Vortrag auf, wie auf modernen Werkzeugmaschinen eine steigende Zahl von Cyber-Physischen Systemen zur Verbesserung der Qualität und zur Erweiterung der Bearbeitungsmöglichkeiten eingesetzt werden kann.
Die EMO Hannover 2019 wird vom 16. bis 21. September 2019 stattfinden.
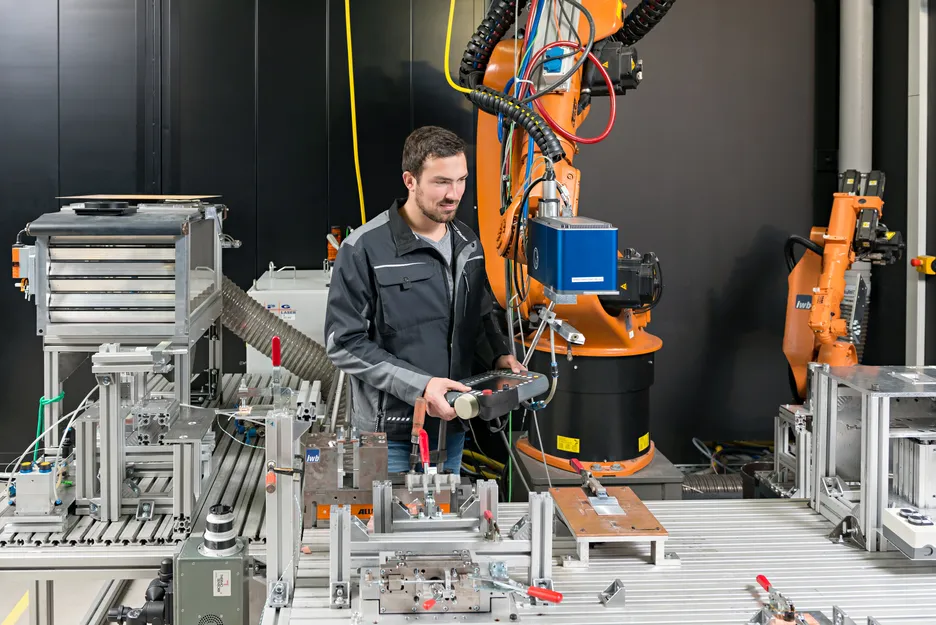
Ob in der Automobilindustrie, im Flugzeugbau oder in der Raumfahrt: Weniger ist mehr, wenn es um die Masse geht. Materialien wie faserverstärkte Kunststoffe und Leichtmetalle bieten die Möglichkeit, Bauteile mit geringerer Masse herzustellen. Eine Herausforderung dabei ist die feste Verbindung der verschiedenen Materialien. Forscher der TU München arbeiten daran, diese Fügetechniken zu optimieren. Unter anderem untersuchen sie die Effizienz der Strukturierung der Metall-Oberfläche durch Laserstrahlung.
Der Leichtbau birgt ein großes Potenzial für die Industrie. Autos und Flugzeuge verbrauchen weniger Kraftstoff, wenn sie leichter sind, und haben daher auch einen geringeren CO2-Ausstoß. Bei Elektroautos ist das Gewicht besonders entscheidend: Je leichter das Auto, desto größer die Reichweite, die mit einer Batterieladung möglich ist. Neben Leichtmetallen wie Aluminium werden zunehmend faserverstärkte Kunststoffe genutzt. Dabei ist es wichtig, das jeweilige Material an der richtigen Stelle einzusetzen. Metalle etwa werden dort benötigt, wo hohe Druckfestigkeit und geringe Elastizität gefordert sind – also zum Beispiel bei Schraubverbindungen. So kommt es bei komplexen Produkten wie dem Automobil zum Einsatz beider Werkstoffe und demensprechend zu Mischverbindungen aus Kunststoff und Metall.
Alternative zu Kleber und Schrauben
Die Herausforderung besteht darin, Kunststoff- und Metallkomponenten möglichst effizient, schnell und stabil zu fügen, also fest miteinander zu verbinden. Bisher wurden die Werkstoffe vor allem durch Klebstoffe gefügt, erklärt Alexander Fuchs vom Institut für Werkzeugmaschinen und Betriebswissenschaften der TUM (iwb). Doch dieser Prozess ist aufwändig. Zunächst muss der Klebstoff dosiert und aufgetragen werden. Während der Klebstoff aushärtet, müssen die Komponenten, die geklebt werden, fixiert sein. Auch die Verbindung der Werkstoffe mithilfe von Schrauben und Nieten hat Nachteile. Denn durch das zusätzliche Material der Verbindungselemente nimmt die Masse der Bauteile zu. Es besteht außerdem die Gefahr, dass die Bohrungen die Struktur schädigen und somit die Festigkeit des faserverstärkten Kunststoffs vermindern.
Oberflächenbehandlung durch Laser
Am iwb wird an Verfahren gearbeitet, mit denen sich Metalle und thermoplastische, also schmelzbare Kunststoffe mithilfe von Wärme hochfest ineinanderfügen lassen. Dafür wird zunächst die Oberfläche des Metalls durch Laserstrahlung strukturiert und mit kleinen Hohlräumen versehen. André Heckert, wissenschaftlicher Mitarbeiter am iwb, untersucht unter anderem, wie verschiedene Laser-Oberflächenbehandlungen die Festigkeit des Kunststoff-Metall-Verbundes beeinflussen. Durch die Laserstrahlung können Strukturen im Bereich von Nanometern bis einigen Millimetern Höhe erzeugt werden. "Welche Oberflächenstruktur die besten Verbundeigenschaften ermöglicht, hängt von den eingesetzten Werkstoffen ab", erklärt Heckert. Er fand heraus, dass ein Rillenmuster von einigen Zehntelmillimetern Tiefe besonders bei Kunststoffen geeignet ist, die mit Kurzfasern verstärkt sind. Feine Oberflächenstrukturen, die durch den Einsatz von gepulsten Lasersystemen generiert werden, sind hingegen besonders effektiv bei sogenannten endlosfaserverstärkten Kunststoffen.
Kurz und schmerzlos: Fügen durch Nanofolien
Nach der Strukturierung mit dem Laser werden Metall und Kunststoff zusammengepresst. Das Metall wird in diesem Zustand erhitzt, bis der Kunststoff schmilzt und die Hohlräume füllt. Nach dem Abkühlen ist eine stabile Verbindung entstanden. Um die für das Fügen nötige Hitze zu erzeugen nutzen die Wissenschaftler drei unterschiedliche Verfahren. Durch Laserstrahlung kann auch die nötige Wärme erzeugt werden, um den Kunststoff zum Schmelzen zu bringen. Beim sogenannten Reibpressfügen wird die Wärmeenergie in Form von Reibung erzeugt. Ein zylindrisches Werkzeug rotiert dazu unter definiertem Druck auf der Metalloberfläche. Eine komplett andere Methode ist das sehr schnelle Fügen mithilfe von reaktiven Nanofolien. Nanofolien erzeugen bei Zündung punktuell sehr hohe Temperaturen von 1000 bis 1500 °C. Diese Hitze wird genutzt, um den Kunststoff und das Metall miteinander zu verbinden. Mit dieser Technologie können zum Beispiel metallische Kabelhalter über eine thermoplastische Zwischenschicht in kürzester Zeit an den Rumpf von Flugzeugen gefügt werden.