Public Relations
On this page, you will find an overview of the previously published press releases from the research and development work of the iwb.
Should you require interview or film dates, photo or text material, our Public Relations Service Center will be pleased to assist you.
The iwb welcomes Prof. Dr.-Ing. Rüdiger Daub as the new Head of the Institute alongside Prof. Dr.-Ing. Michael F. Zäh as of June 01, 2021.
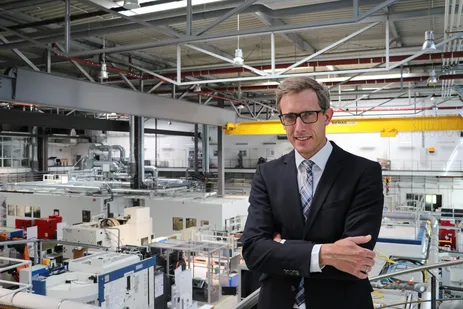
Effective June 01, 2021, Prof. Dr.-Ing. Rüdiger Daub succeeds Prof. emeritus Dr.-Ing. Gunther Reinhart, who retired in October 2020, as Head of the Institute of Machine Tools and Industrial Management (iwb) at the Technical University of Munich. As full professor of the newly established Chair of Production Technology and Energy Storage Systems at the iwb, Rüdiger Daub will thus support Prof. Dr.-Ing. Michael F. Zäh in the institute's management. In a new cooperation model in joint appointment with the Fraunhofer Gesellschaft, he thus assumes responsibility for battery research at the iwb. With his many years of experience in battery cell production at BMW, Mr. Daub will now primarily drive research in this area at the institute in the future.
After almost ten years in industry, Prof. Dr.-Ing. Rüdiger Daub will return to research on June 01, 2021. His appointment as full professor of the newly established Chair of Production Engineering and Energy Storage Systems at the institute is preceded by many years of experience both at the iwb itself and in the field of battery cell production: Rüdiger Daub received his doctorate from the Institute of Machine Tools and Industrial Management in 2012 and joined the BMW Group in the area of technology development and prototype construction directly after his doctorate. Most recently, as Head of Technology Development and Prototype Construction, he was responsible for the production of lithium-ion electrodes.
Alongside Prof. Dr.-Ing. Michael F. Zäh, full professor of the Chair of Machine Tools and Manufacturing Technology, Prof. Dr.-Ing. Rüdiger Daub will now set new priorities in this increasingly important research topic at the iwb from June 01, 2021. "The appointment process was a lengthy one, so we were all the more pleased at the beginning of the year when we learned about the succession by our former research associate Mr. Daub - this is a great win for our institute, both professionally and personally," says Prof. Dr.-Ing. Michael F. Zäh. Rüdiger Daub succeeds Prof. em. Dr.-Ing. Gunther Reinhart, who headed the iwb for 27 years and during this time built up the scientific area of processing technology at Fraunhofer IGCV, which Mr. Daub will also be leading.
Strong weld joints for aerospace applications
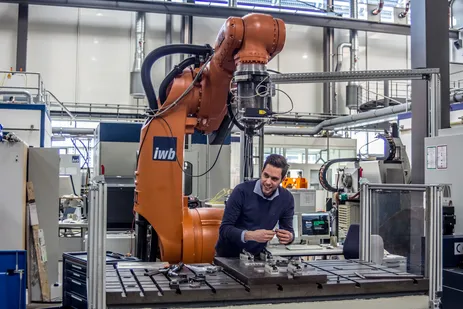
Measurements at the Research Neutron Source help with the development of intelligent welding equipment
When a rocket is launched, the weld seams on the enormous fuel tanks must withstand immense forces. To produce joints with the necessary strength, a process known as “friction stir welding” is used. Scientists at the Technical University of Munich (TUM) are working to make this process more efficient. They are using positrons generated by the Research Neutron Source Heinz Maier-Leibnitz (FRM II) to precisely localize “atomic holes” in the material.
The friction stir welding process is increasingly common in applications requiring particularly strong and leakproof joints such as aircraft fuselages, automotive cooling systems or rocket fuel tanks. In contrast to other welding processes, friction stir welding requires no additional consumable materials and temperatures generally remain below the melting point of the workpieces. Consequently, the process is especially suitable for heat-sensitive materials such as aluminum.
Once the workpieces are clamped in place, the rapidly rotating welding pin is moved along the joint between the materials. The pin softens the material through frictional heat without melting it. While moving forward, the pin intermixes the two workpieces at the joint, producing a strong joint after cooling.
The problem with this process, invented just 30 years ago, is a lack of empirical data. With every new component and material, the equipment setup needs to be redefined through trial and error. An automatic control system that would select and adjust the settings itself would enormously improve the efficiency of the process. With that goal in mind, Dr. Andreas Bachmann has developed a control concept in his research work at TUM.
Positrons detect “holes” in metal
Bachmann began by working with a special aluminum alloy used in aerospace applications to analyze the influence of temperature and welding speed on the process. To do so, he used NEPOMUC, the world’s most intense positron source, at the Research Neutron Source Heinz Maier-Leibnitz (FRM II). “Using coincident doppler-broadening spectroscopy (CDBS) we were able to find flaws in the metal in and near the weld joint,” says Bachmann.
In the CDBS method, the researchers fire positrons into the metal lattice. There they are repelled by positively charged atomic nucleii and find their way into vacancies (“holes”) where they meet their antiparticle, the electron. This results in electron-positron annihilation and the creation of energetic photons. The measurements of the detected photons provide information on the position and frequency of atomic vacancies.
Defects are linked to temperature
Fewer defects at higher welding temperatures of around 500°C were detected. “However, 500°C is still very low compared to other welding processes,” says Bachmann. “That shows: a lower welding temperature is naturally better for these temperature-sensitive materials. But if it is too low, however, it has a negative impact on the strength of the weld.” The ideal welding temperature may differ for other materials and must be determined on a case by case basis.
Bachmann has used these insights to develop a control for setting the optimal temperature. A sensor measures the temperature in real time. An algorithm determines how fast the tool needs to rotate so that the deviation between the target and actual values is 0. “Using the control, a weld joint was 1.5 times stronger in the test than without it,” says Bachmann.
He also showed that it would be theoretically possible to regulate the welding process without additional temperature sensors by measuring the resistance to the rotating welding pin to determine the temperature. “The hotter the metal, the easier it is to shape it -- or stir it with the tool,” says Bachmann, who is now working in industry. “We can measure how easy or hard it is to stir the metal via the mechanical load on the spindle, i.e. the motor, driving the tool.” This approach could be refined to make it easier to use this control method in industry.
Publications:
Bachmann, A.; Gigl, T.; Hugenschmidt, C. P.; Zaeh, M. F.: Characterization of the microstructure in friction stir welds of EN AW-2219 using coincident Doppler-broadening spectroscopy. In: Materials Characterization 149, (2019), S. 143 – 152. doi.org/10.1016/j.matchar.2019.01.016
Source: TUM Corporate Communications Center
Press Release
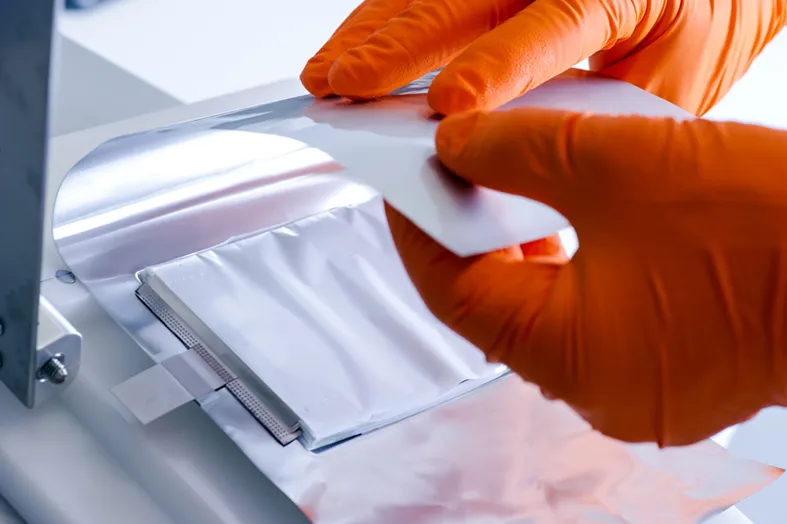
As of July 01, 2019, the Institute for Machine Tools and Industrial Management (iwb) at the Technical University of Munich was expanded to include the "Battery Production" topic group. This bundles and further expands the competence in battery research. With already 11 employees, the new thematic group focuses on the same goals that the German government is pursuing - strengthening tomorrow's battery research and production.
High-performance electrochemical energy storage systems are of great importance for applications in electromobility and stationary energy storage. Improving gravimetric and volumetric energy density and reducing production costs are crucial for this. Only a deeper process understanding of lithium-ion battery (LIB) manufacturing enables the production of improved and cost-effective battery cells.
The Battery Production topic group, which was newly established in July 2019, focuses on the production of innovative battery cells. The core of the work is process development and optimization of all processes within battery production. From the mixing of electrode materials to the formation of the finished cells and battery module assembly, all steps are performed in-house at the iwb's research production line. The main research topics of the battery production group are:
- Electrode design and production
In the research field of electrode design and production, the staff is intensively involved in new electrode designs (from slurry formulations to electrode structures) and the processing of novel electrode materials. On the cathode side, research focuses primarily on low-cobalt materials based on NMC, NCA and prelithiated manganese-rich high-voltage spinels. For anode materials, the research focus is on silicon composites and the prelithiation of anodes.
- Cell production and quality
The research field Cell Production and Quality deals intensively with cell assembly and the characterization of large-format battery cells. At the iwb, research is conducted on the process steps of electrode cutting (laser cutting and punching), automated stack formation, contacting, electrolyte filling and forming. In order to be able to guarantee high productivity along the process chain, good quality at low cost, the iwb relies on innovative quality assurance methods and data-based process monitoring.
The lighter the better. That is the golden rule, at least in the automobile, aircraft and aerospace industries. Materials like fiber-reinforced plastics and light metals are paving the way for components with lower densities. The firm and secure fusion of different materials poses a major challenge, however, which is why researchers from the Technical University of Munich (TUM) are working on ways to improve joining techniques - for example by laser surface treatments.
Lightweight fabrication techniques offer huge potential for industry. Lighter automobiles and aircraft require less fuel, thereby reducing their CO2 emissions. Weight is a particularly important factor in electric cars, as the lighter the vehicle, the greater its range on a single battery charge. Fiber-reinforced plastics are increasingly complementing light metals such as aluminum. Success lies in putting the right material in the right place. Metals are ideal where strong resistance to pressure and low elasticity are required – in screwed connections for example. But in complex products like automobiles, plastics are used alongside metals and both materials need to be joined together at certain points.
Alternative to adhesive and screws
The challenge lies in forming a firm and stable bond between plastic and metal components as efficiently and quickly as possible. "Up until now, adhesives were the favored means of achieving this", Alexander Fuchs from TUM’s Institute for Machine Tools and Industrial Management (iwb) explains. The downside of this process is that it is time-consuming. First of all, the adhesive has to be metered and applied. Then while it is hardening, the components have to be held securely in place. Joining metal and plastic with screws and rivets also has downsides. The connection pieces add extra weight to the component. In addition, there is a risk that the holes will damage the structure and reduce the resistance of the fiber-reinforced plastic.
Laser surface treatment
The iwb is optimizing processes to securely fuse metals and thermoplastic (meltable) plastics by applying heat. The first stage involves texturing the metal surface with a laser beam, producing tiny hollows. André Heckert, doctoral candidate at iwb, is looking at how different laser surface treatments influence the strength of the plastic-metal bond. Laser treatment can produce structures with a depth ranging from nanometers to a few millimeters. "The choice of surface structure for the best bonding properties depends on the material in question," explains Heckert. He has discovered that a groove pattern a few tenths of a millimeter deep is particularly suitable for plastics reinforced with short fibers. By contrast, fine surface structures, which are generated with pulsed laser systems, are highly effective in the case of continuous fiber-reinforced plastics.
Quick and easy joining with NanoFoil
After the laser texturing stage, the metal and plastic materials are pressed together. The metal is now heated until the plastic melts and flows into the hollows. On cooling, a stable bond is formed between the two materials. The scientists are using three different methods to create the necessary heat. Here again, a laser beam can generate enough heat to melt the plastic. In friction press joining, thermal energy is created by the friction of a cylindrical tool rotating on the metal surface under a defined pressure. A completely different and very quick method relies on NanoFoil technology. When it ignites, NanoFoil can briefly reach a temperature as high as between 1,000 and 1,500 °C. This heat bonds the plastic and metal together. One possible application for this technology could be the fast joining of metal cable clips to an aircraft fuselage via a thermoplastic intermediate layer.